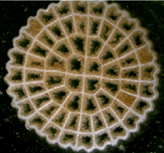
Unique selling points
- Smaller footprint compared to the activated sludge process
- No sludge recirculation required
- Suitable for retrofitting existing plants
- No clogging
- High adaptability of microorganisms possible due to long sludge retention times and removal of complex organic compounds
Description of the technology
The moving bed biofilm reactor (MBBR) is a biofilm process that provides plastic carriers for microorganisms to grow on. These carriers are constantly kept in suspension in the moving bed reactor by the water movement and/or aeration. The desired flow profile in the reactor ideally corresponds to a fully mixed stirred tank. The use of the moving bed biofilm process has proven effective for nitrification, denitrification as well as for BOD removal (full and partial purification). After the MBBR, washed out biomass can settle in the secondary clarifier. Compared to the activated sludge process, however, no return activated sludge is needed.
Flow scheme of the technology
Source: DWA-DVWK-Arbeitsgruppe IG-5.6 „Biofilmverfahren“, Aerobe Biofilmverfahren in der Industrieabwasserreinigung - Definitionen, Verfahrenstechniken, Einsatzgebiete, Bemessungshinweise, 2005
Technology requirements and operating conditions
As a biofilm process, it is commonly accepted, that the performance of a MBBR primarily depends on the surface area for biofilm growth instead of the reactor volume. To effectively calculating the biofilm area, the specific area of the carriers (m²/m³) and the level of filling in the reactor are necessary. Both are the two main design parameters for MBBRs. There is a variety of different carriers on the market with specific surface areas ranging from 190 to 690 m²/m³ (figure 1). The filling volume is usually between 30 - 70 % (Rodgers, M., Zhan, XM. Moving-Medium Biofilm Reactors. Re/Views in Environmental Science and Bio/Technology 2, 213–224 (2003). https://doi.org/10.1023/B:RESB.0000040467.78748.1e).
Figure 1: Examples of carriers as used by Odegaard et al. 2000 (Source: H. Ødegaard; B. Gisvold; J. Strickland, The influence of carrier size and shape in the moving bed biofilm process, Water Sci Technol (2000) 41 (4-5): 383–391., https://doi.org/10.2166/wst.2000.0470)
To keep the carriers suspended, an adequate mixing device and/or aeration depending on the application (BOD removal, denitrification) is required. Depending on the application, some design parameters are given in table 1. However, they should be regarded as indicators, as they strongly depend on the application.
Table 1: Design of MBBRs for different applications
Application |
Range for use as post-treatment |
Reference |
BOD removal |
15 - 20 kg BOD/(m2*d)
< 10 kg COD/(m³*d) 4.5 - 6.0 kg BOD/(m³*d) |
(Tchobanoglous et al. 2014 5th Edition, ISBN 978-0-07-340118-8 |
Nitrification |
0.4 - 1.4 kg NH4-N/(m²*d)
0.1 - 0.4 kg NH4-N/(m³*d) |
|
Post-Denitrification |
1.0 - 2.0 kg NO3-N/(m³*d)
0.3 - 0.6 kg NO3-N/(m³*d) |
|
pH |
6 - 8,5 |
|
Temperature |
10 - 35 °C |
|
Oxygen concentration |
2 - 3 mg/L (optimum) |
(Rodgers, M., Zhan, XM. Moving-Medium Biofilm Reactors. Re/Views in Environmental Science and Bio/Technology 2, 213–224 (2003). https://doi.org/10.1023/B:RESB.0000040467.78748.1e) |
Key performance indicators
- Removal efficiency of organic matter [%]
- Removal efficiency of ammonium, nitrate