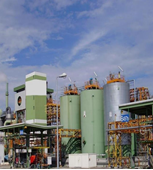
Unique selling points
- Allowing for treatment of high sulphur waste
- Removal of SO2 from fumes reaching legislative requirements
- Recovery of Sodium Bisulphite
- Circular economy system
Description of the technology
The exhaust gases from waste incineration facilities may contain many potentially harmful substances. Particularly, sulphur will produce sulphur oxides (SOx) in the flue gases (National Research Council, 2000). Acid gases cause widespread damage when they precipitate as acid rain or when they form weak acidic solutions with moisture at ground level. Consequently, SO2 emission standards have been introduced in many countries on a national and regional basis (Falcone Miller & Miller 2010) and are decreasing all over the world (Lestinsky et al. 2017).
The reduction of SO2 emissions is achieved by installing a flue gas desulfurization system. There are two categories of recovery processes which varies as a function of generated by-products. First, processes called “regenerative”, which allow to generate elementary sulphur or sulphuric acid by absorption of sulphur dioxide (Jacubowiez et al. 2000). Then, processes called “non-regenerative”, involve the formation of different by-products, generally associated to oxidated components like sulphate or gypsum (Lunt et al. 2000, Jacubowiez et al. 2000).
In the Roches-Roussillon chemical platform, SUEZ IWS Chemicals has developed the range of waste received, with the treatment of high-sulphur waste. They now want to upgrade the current (non-regenerative) process to a recovery solution. The chosen recovery process must adapt to constraints imposed by the composition and characteristics of effluents. Generally, scientific works published past few years discuss more simple systems or only mention desulfurization without talking about recovery (Wang et al. 2015, Chang et al. 1985, Zeicht et al. 2020).
The process developed is based on a patent (Hustache et al. 2001). It has the objective of removing the SO2 from the fumes producing Sodium Bisulphite. Sulphur dioxide is a strong acid gas (Vanderschuren et al. 2010) which forms bisulfite ion (HSO3-) in aqueous solutions at a pKa level of 1.9, and sulfite ion (SO32-) at a pKa level of 7.2. The pH level will therefore be an essential parameter to obtain the target product. Sodium bisulphite has many commercial uses including as disinfectant, bleaching agent and as mild reducing agent for removal of small amounts of chlorine, bromine, iodine, hypochlorite salts and oxygen (i.e. an oxygen scavenger agent) (Kisielewski et al. 2011).
The industrial pilot was designed from this process. It is composed of a heat exchanger allowing to condense fumes, of two absorption columns regulated at different pH level by soda addition for SO2 absorption and of a storage tank for the target product (cf. Flow Scheme of the technology).
Flow scheme of the technology
Synergetic effects and motivation for the implementation of the technology
- High removal efficiencies for a wide range of inlet SO2 levels;
- Tolerant of wide fluctuations in inlet SO2;
- Generation of an interesting by-product;
- Material recovery;
- Establishment of a system promoting a circular economy.
Technology requirements and operating conditions
Tab. 1 Typical ranges for operating parameters
Parameter |
Units |
Min |
Max |
Reference |
% SO2 in flue gas |
% |
0,1 |
2 |
ULTIMATE |
pH |
- |
3 |
8.5 |
ULTIMATE |
Temperature |
°C |
ambient |
80 |
ULTIMATE |
Oxygen content in flue gas |
% |
2.0 |
10.0 |
ULTIMATE |
Case Study applying the technology
Publications
- Chane-Ching J.Y., Hustache G., Sabot J.L., Procédé de traitement d'un effluent gazeux contenant de l'anhydride sulfureux, 1994
- Chang C.S., Rochelle G.T., Sulfur dioxide absorption into sodium hydroxide and sodium sulfite aqueous solutions, 1985
- Falcone Miller, S., Miller. B.G., Advanced flue gas cleaning systems for sulfur oxides (SOx), nitrogen oxides (NOx) and mercury emissions control in power plants., 2010
- Jacubowiez I., Désulfuration des fumées, 2000
- Kisielewski, J., Robertson, D., Process for production of Sodium Bisulfite, 2011
- Lestinsky, P., Jecha, D., Brummer, V., Stehlik, P., Wet flue gas desulphurization using a new O-element design, 2017
- Lunt, R.R., Little, A.D., Cunic, J.D., Profiles in Flue Gas Desulfurization, 2000
- National Research Council (US) Committee on Health Effects of Waste Incineration, Waste Incineration & Public Health
- Vanderschuren J., Thomas D., SO2 (oxydes de soufre)., 2010
- Wang Z., Peng Y., Ren X., Gui S., Zhang G, Absorption of sulfur dioxide with sodium hydroxide solutions in spray column, 2015
- Zeicht P.M., Mengel M., Hammer M.T., Ammonia-based flue gas desulfurization system and method, 2020