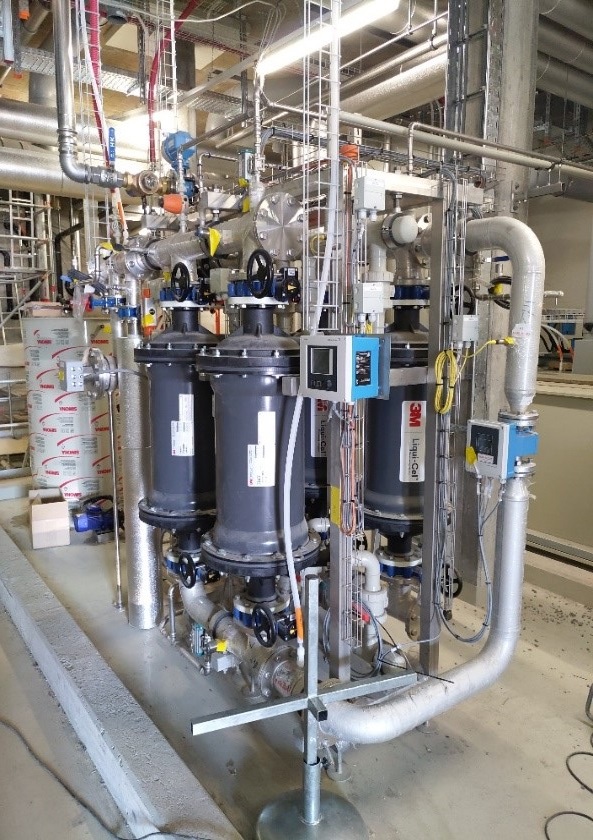
Unique selling points
- High ammonia recovery rates related to the influent to the recovery unit of up to 99%
- Market-ready product: ammonium sulphate solution as liquid fertilizer
Description of the technology
Ammonia is a key component for fertiliser production, while ammonia and related compounds in wastewater streams have adverse effects on the receiving water such as algal blooms and toxicity problems. The hollow fibre membrane contactor (HFMC) technology is promising for the recovery and removal of ammonia via stripping from highly-concentrated wastewater flows.
The HFMC is usually implemented at WWTPs for 100 000 population equivalents and more for a side stream treatment of sludge liquor after anaerobic digestion. Before ammonia membrane stripping can be applied, several pre-treatment steps have to be conducted in order to remove particulate matter and residual organics from the sludge liquor and to reach the required elevated pH and temperature (see Requirements of the technology). At higher pH and temperature, ammoniacal nitrogen is mainly present as gaseous ammonia (NH3).
The pre-treated liquor flows through the HFMC containing hollow fibre membranes (see Flow scheme of the technology). Those membranes are hydrophobic and gas permeable with a pore size of between 10-3 and 1 µm. The HFMC has two channels: inside of the hollow fibres (lumen side) and outside of the hollow fibres (shell side). Due to differences in the ammonia partial pressure across the membrane during operation, the ammonia gas is released from the liquor at the shell side and diffuses to the lumen side. In the lumen side, it reacts with sulphuric acid to liquid ammonium sulphate.
Ammonium sulphate solution is a typical nitrogen fertiliser which can be directly used by the farmers. Typical N concentrations in the product of membrane stripping units range from 19 to 60 kg/m³ of nitrogen (Böhler et al. 2018). Due to the defined composition of the product, the relative fertilizer efficiency is similar to commercially available ammonium sulphate (Szymańska et al. 2019).
Flow scheme of the technology
Pictures
Synergetic effects and motivation for the implementation of the technology
- Reduction of the nitrogen return load of a WWTP
High loads of nitrogen in sludge liquor put an additional burden on the WWTP when returned to the plant inlet (“return load”). Membrane stripping of ammonia from sludge liquor can help to reduce this return load significantly, saving on aeration energy and treatment capacity of the mainline WWTP.
- Production of a contaminant-free fertilizer
The hollow fibre membrane contactor allows for the production of ammonium sulphate with a very high quality, resulting in a contaminant-free fertilizer. The gas-permeable membrane acts as a physical barrier for any contaminant present in the liquor.
- Reduction of formation of N2O in the biological step
Reducing the nitrogen return load to the mainline will stabilize the nitrogen removal and helps to prevent overloads of the treatment capacity. As high nitrogen loads and high fluctuations often lead to higher emissions of N2O from the activated sludge process, membrane stripping will also lead to a decrease in emissions of this potent greenhouse gas.
Technology requirements and operating conditions
In order to reach high ammonia yields, the fraction of ammonium in relation to the total nitrogen content should be as high as possible. Anaerobic digestion combined with a pre-treatment of sludge such as a thermal hydrolysis process can help to improve degradation of organic compounds, resulting in an increase in ammonium concentrations and thus a higher recovery potential.
Several pre-treatments steps for the total removal of solids and particles are an obligatory prerequisite for the application of ammonia stripping membranes, as the membrane tolerance to particles in the influent is very low. Furthermore, temperature and pH need to be increased prior to the stripping process to shift the chemical equilibrium from ammonium (NH4) to free ammonia (NH3). Thus, in order to increase the pH with minimum chemical demand, CO2 is stripped out from the liquor in a first step (see Flow scheme of the pre-treatment technologies). Depending on the chemical composition of the liquor, CO2 stripping can increase the pH up to 0.4 units, and the buffering capacity of CO2 is also removed (Böhler et al. 2018). The pH is then further elevated up to a pH of 10 via dosing of sodium hydroxide in order to maximize the free ammonia fraction. To prevent fouling and clogging of the membranes, the process is followed by a flocculation and sedimentation step, a sand filtration and finally a cartridge filtration step. Finally, the temperature is increased with heat exchangers. Besides the efficient design of the multi-stage pre-treatment process for particle removal, a major challenge is to find the optimum operating point with a maximised nitrogen recovery at a reasonable demand of chemicals and/or heat. Depending on the type of membrane module, the temperature of the influent liquor should be limited to prevent thermal decomposition of membrane potting. Therefore, Böhler et al. 2018 usually operated the process at 40 °C. However, according to the manufacturer a maximum temperature of 50 °C is still possible, but should not be exceeded (Membrana 2021).
Parameter |
Units |
Min |
Max |
Reference |
NH4 (influent) |
mg/L |
700 |
>4000 |
Huang et al. 2020, Böhler et al. 2018, NextGen D1.5 (in prep.) |
Total suspended solids |
mg/L |
0 |
1000 |
NextGen D1.5 (in prep.) |
pH |
- |
9 |
10 |
Böhler et al. 2018 |
Temperature |
°C |
14 |
50 |
Böhler et al. 2018, Membrana 2021 |
Velocity of feed streams |
m/s |
0.3 |
2.0 |
NextGen, D1.5 (in prep.) |
Flow scheme of the pre-treatment technologies
Key performance indicators
Parameter |
Units |
Min |
Max |
Reference |
N-recovery rate (related to the influent to the nitrogen recovery unit) |
% |
70 |
99 |
Links to related topics and similar reference projects
Ammonium sulphate production processes |
Medium |
Reference |
with membrane stripping (HFMC) |
Liquor |
Case study “Altenrhein” (NextGen); Case study “Spernal” (NextGen) |
Liquor |
||
with vacuum degasification |
Sludge |
Circular Agronomics: D3.1, Chapter 3 (Kleyböcker et al. 2020) |