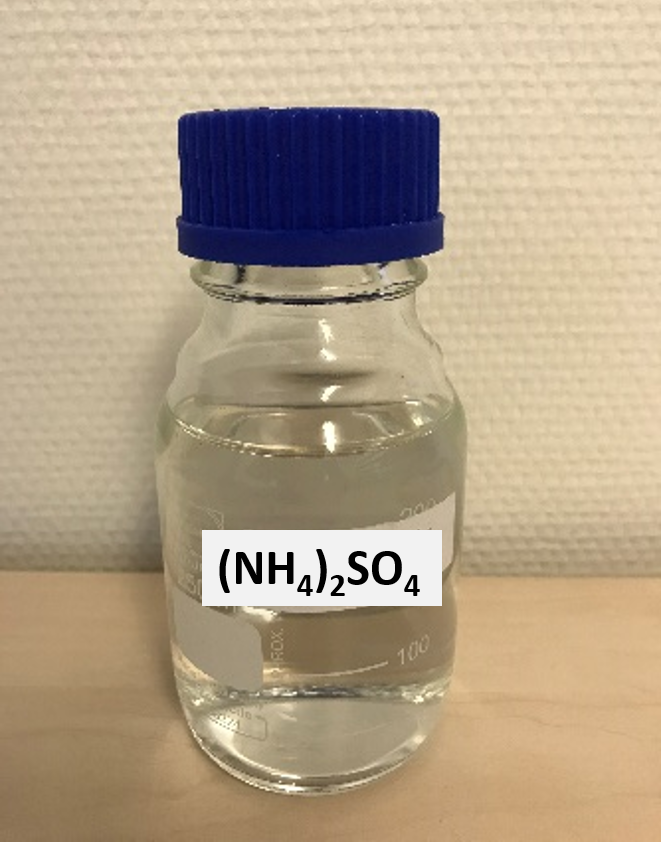
Unique selling points
- High ammonia recovery rates related to the ammonium influent to the recovery unit between 80% and 98%
- Market-ready product: ammonium sulphate solution as a liquid fertiliser
Description of the technology
Nitrogen is one of the main nutrients contained in wastewater. In wastewater treatment, nitrogen is usually removed biologically via nitrification and denitrification. There, the nitrogen is emitted into the air. The process described here relies on physico-chemical reactions and offers the opportunity to recover the nitrogen in the form of ammonium sulphate solution. The process is usually applied to ammonium rich streams such as sludge liquor with also great potential for industrial wastewaters. This process is usually applied at wastewater treatment plants with a capacity of 100 000 population equivalents and greater.
In order to produce ammonium sulphate solution, two columns are used in sequence. The first column is the ammonia stripping unit. Here, the ammonium rich liquor is stripped with air at a temperature between 55 °C and 65 °C and at a pH between 9 and 11. The higher the temperature is and the higher the pH is, the more the equilibrium between ammonium and ammonia shifts to the ammonia side. In order to increase the pH to alkaline conditions, carbon dioxide is stripped from the liquor and/or sodium hydroxide is added. Under those conditions, ammonium is converted to ammonia and can be desorbed from the liquid, into the gas phase, via air stripping. In a subsequent gas scrubber, that is the second column, the obtained ammonia gas reacts with a sulphuric acid solution to form ammonium sulphate, recovered in the liquid phase. Hereby, the ammonia free air can be reused and is injected in the air stripper again. The relation of the air flow to the liquor flow in the stripping unit is a pivotal parameter for the ammonia removal performance and can be from around 500, up to 2000-3000.
Ammonium sulphate solution is a nitrogen fertiliser. Typical concentrations are 37 – 40 % of ammonium sulphate in water. According to Szymańska et al. 2019, the reference fertiliser efficiency describes the effectiveness of the ammonium sulphate produced by such a system compared to that of commercially available ammonium sulphate. Both are in a similar range, the reference fertiliser efficiency of the recovered ammonium sulphate solution is between 89 and 103% of that for commercial ammonium sulphate depending on the plant and soil type.
Flow scheme of the technology
Pictures
Synergetic effects and motivation for the implementation of the technology
- Robust process
In contrast to the microbial nitrogen removal via nitrification and denitrification, the nitrogen removal via stripping and scrubbing does not rely on microorganisms and thus, the process is very robust.
- Reduction of formation of N2O in the activated sludge process of the WWTP
Reducing the nitrogen return load to the mainline will stabilize the nitrogen removal and helps to prevent overloads of the treatment capacity. As high nitrogen loads and high fluctuations often lead to higher emissions of N2O from the activated sludge process, air stripping will also lead to a decrease in emissions of this potent greenhouse gas.
Technology requirements and operating conditions
In order to reach high ammonia yields, the fraction of ammonium in relation to the total nitrogen content should be as high as possible. Up to now, the process was applied for concentrations between 800 and 4000 mg NH4-N/L. However, technically a lower concentration is also feasible. In this case, it should be investigated, if the process can be still operated economically. Anaerobic digestion combined with an additional thermal pressure hydrolysis can help to lyse and degrade organic compounds resulting in an increase in ammonium concentrations.
Parameter |
Units |
Min |
Max |
Reference |
NH4-N process water feed |
mg/L |
800 |
4000 |
|
DM process water feed |
% |
- |
2 |
NextGen D1.5 (in prep.) |
TSS process water feed |
mg/L |
- |
600 |
|
pH |
- |
8 |
11 |
|
Temperature |
°C |
55 |
65 |
Key performance indicators
Parameter |
Units |
Min |
Max |
Reference |
N-recovery rate (influent nitrogen recovery unit) |
% |
80 |
98 |
NextGen D1.5 (in prep.) |
N-recovery rate (influent WWTP) |
% |
10 |
20 |
Links to related topics and similar reference projects
Ammonium sulphate production processes |
Medium |
Reference |
with air stripping |
Liquor |
|
with air stripping | Distillery wastewater | Case study 7 in Tain, UK (ULTIMATE) |
with membrane stripping |
Liquor |
Case study “Altenrhein” (NextGen), Case study “Spernal” (NextGen) |
with vacuum degasification |
Sludge |
Circular Agronomics: D3.1, Chapter 3 (Kleyböcker et al. 2020) |
Case Studies applying the technology
Publications
- Böhler, M., Büttner, S., Liebi, C., Siegrist, H., Ammoniakstrippung mittels Luft zur Behandlung von Faulwasser und Urin auf der auf der Kläranlage Kloten/Opfikon, 2012
- Kleyböcker, A., Kenyeres, I., Poor-Pocsi, E., Nättorp, A., Loreggian, L., Schaub, M., Egli, C., Grozavescu, M., Murariu, M., Radu, B., Scheer, P., Lindeboom, R., Giurgiu, R., Suters, R., Heinze, J., Soares, A., Vale, P., Kim, J., Lanham, A., Hofman, J., D1.5 (2022) New approaches and best practices for closing materials cycle in the water sector, 2022
- Kleyböcker, A., Kraus, F., Moermann, W., Pudova, N., Holba, M., Dünnebeil, A., Efficient carbon, nitrogen and phosphorus cycling in the European agri-food system and related up- und down-stream processes to mitigate emissions, 2020
- Szymańska, M., Sosulski, T., Szara, E., Wąs, A., Sulewski, P., van Pruissen, G., Cornelissen, R., Ammonium sulphate from a bio-refinery system as a fertilizer - agronomic and economic effectiveness on the farm scale, 2019