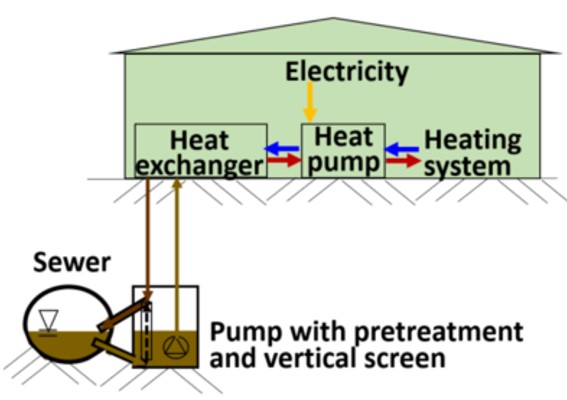
Unique selling points
- Heat recovery or cold air generation
- Energy-efficient alternative to boilers or air conditioners
Description of the technology
Domestic wastewater usually contains heat, mainly from processes operated at warm temperatures, such as showering, clothes washing and dishwashing. This heat can be recovered either within houses in small-scale applications, from the sewer in small-scale (5 kW – 150 kW) to medium-scale applications (150 kW – 700 kW) or at wastewater treatment plants in large-scale applications. The further away from the heat source, the more energy will be lost into the environment.
Here, the focus is put on the medium-scale application. Wastewater entering the sewer system has usually a temperature between 10 °C and 20 °C or even more depending on its source and on the outdoor temperature. The available heat varies over time due to temperature and flowrate variations. The heat is recovered via a heat exchanger located in or near the sewer (Fig. 1). The heat exchangers transfer the heat from the wastewater to a closed heat exchange loop. The heat medium in the loop is typically water. Usually, plate heat exchangers or shell-and-tube heat exchangers are applied. The heat exchanger is coupled to a heat pump. The heat pump abstracts the thermal energy at an elevated temperature enabling its reuse for heating purposes, e.g. of a nearby building.
In summer, the heat pump can also be operated reversely in order to cool a building and thus, (partly) substitute a conventional air conditioner. The heat collected from the environment by the heat pump is transferred to the wastewater. Compared to an air conditioner or a boiler, a heat pump is much more energy efficient. Nevertheless, to enable space heating in a building, the heating system in the building needs to be adapted to low-temperature heating systems.
In the NextGen case study Athens, the heat is recovered in a sewer mining unit that includes a membrane bioreactor (Fig. 2). The treated wastewater effluent from the membrane bioreactor (MBR) is used for heat recovery. The effluent has a temperature between 15 °C and 20 °C. The contained heat is recovered from the effluent via a heat exchanger in the wastewater effluent tank. The heat exchanger transfers the heat from the wastewater to a circulating water. The heat exchanger is coupled to a heat pump (Fig. 3). The heat pump increases the heat for pre-heating of the incoming mixture to the rapid composting bioreactor unit.
In Ultimate, the heat from the effluent of an anaerobic membrane bioreactor (AnMBR), which treats distillery wastewater, is suitable to be recovered. The effluent has a temperature of 35-38 °C. At the case study in Tain, different reuse options for the recovered heat are investigated (Fig. 3). One option is to use the heat for the stripping process of the ammonia from the AnMBR effluent. The advantage is that the equilibrium between ammonium and ammonia shifts to the ammonia side with increasing temperature. Hence, a higher process temperature leads to a higher ammonia yield of the stripping process. The other option is to reuse the heat to increase the temperature of the nutrient-depleted liquor that will be post-treated via reverse osmosis. The benefit would be a lower dynamic viscosity due to the higher temperature. This results in a higher flux and hence, a higher water recovery efficiency. However, a potential drawback might be a higher fouling capacity due to a higher microbial activity in the warmer liquor.
Flow scheme of the technology
Three different cases of heat recovery from wastewater and treated wastewater are shown in this section. Fig. 1 presents the case, in which low-grade heat is recovered directly from the wastewater in a sewer system. Fig 2 refers to the NextGen project, where heat is recovered from the effluent of a membrane bioreactor. The heat is reused to temper a rapid composting unit. Fig. 3 refers to the Ultimate project, in which the heat from an AnMBR is considered to be reused, and different options for its reuse are tested as described in the section “Description of the Technology”.
Fig. 1 Thermal energy recovery: a) outside the sewer and b) inside the sewer
Fig. 2 NextGen project (case study Athens): sewer mining unit with the thermal energy recovery from the effluent of the membrane bioreactor (MBR)
Fig. 3 Ultimate project (case study Tain): points of application for heat utilisation in the treatment train for distillery wastewater
Synergetic effects and motivation for the implementation of the technology
- Energy efficient heating and cooling dependent on the season
The heat pump uses available excess heat as an energy source and thus, its energy efficiency is much higher than a conventional air conditioner or a boiler. Depending on the conditions such as temperatures etc., the heat recovery system can replace cooling and heating units operated with fossil fuels.
- Thermal energy storage
Recovery of the heat and the demand for heat will not always occur in the same time. Often it is required to store the heat. For smaller systems, water tanks or phase transition heat storage systems can be used. For larger systems, aquifer theraml energy storage (ATES) systems can provide an adequate solution. The latter also allow longer-term seasonal storage.
Technology requirements and operating conditions
The heat recovery efficiency in a sewer relies on different parameters. Those are the flow rate and temperature in the sewer, the temperature difference of the wastewater upstream and downstream of the heat exchanger and the geometry of the pipe and heat exchanger. In addition, the viscosity of the wastewater, the velocity of the fluids in the heat exchanger, the heat transfer resistance caused by biofilm formation, the heat exchange coefficient and the heat transfer surface area play a major role. According to Brunk et al. 2013, the flow rate in the sewer should be at least 15 L/s with a sewer diameter of at least 800 mm for such a system. However, Brandenburger Liner (2021) indicate minimum diameters of 300 mm and flow rates of at least 8 L/s. In general, the necessary flow rate and diameter depend highly on the certain technology which will be applied. For example, in Bologna flow rates between 200 and 400 L/s were used (Cipolla and Maglionico 2014) and in Brno (Czech Republic), the flow rates ranged between 130 L/s and 470 L/s (Cecconet et al. 2019).
When heat recovery is applied, the temperature of the wastewater should not be reduced below 10 °C. If the temperature in the wastewater decreases below 10 °C, the biological purification processes might be affected negatively in wastewater treatment plant (Wanner et al. 2005). Simultaneously, this would lead to an increase in its energy demand. Thus, before planning such a heat recovery unit, it should be carefully investigated which temperature will result in the influent to the corresponding wastewater treatment plant. Hereby, mixing effects with warmer flow streams might neglect the effect of the heat recovery in a certain sewer. Elías-Maxil et al. (2017) and Bailey et al. (2020) have developed modelling tools to predict heat availability and temperatures in sewer networks.
Parameter |
Units |
Min |
Max |
Reference |
Sewer pipe diameter: Circular profile Oval profile |
mm |
300 250/375 |
1300 1300/1950 |
Brandenburger Liner 2021 |
Flow rate
|
L/s |
8 |
470 |
|
Length of sewer with a straight line |
m |
20 |
200 |
|
Temperature of wastewater before heat extraction |
°C |
10 |
- |
|
Temperature after heat extraction in the influent to a WWTP |
°C |
10 |
- |
Key performance indicators
The heat recovery system consists of the heat exchanger in the sewer and the heat pump. Thus, there are at least two key performance indicators to be considered. The performance of the heat exchanger is usually indicated as heat transfer efficiency or heat transfer coefficient. It should be noted that the wastewater may lead to the formation of a biofilm on the heat exchanger. That can diminish its heat transfer efficiency. According to Brunk et al. 2013, the biofilm can function as an insulating layer between the wastewater and the heat exchanger, depending on its thickness. This can lead to a decrease in the temperature difference of up to 5 K. Besides biofilm formation, scaling and corrosion processes can also contribute to a decrease in the heat transfer efficiency of heat exchangers. In practise, to overcome the fouling effect, either the heat exchangers have an oversized surface or anti-fouling surfaces are used for the heat exchangers.
For the heat pump, the coefficient of performance (COP) is defined as the ratio of the discharged thermal energy and the sum of the thermal and electrical energy charged to the heat pump. Here, the temperature difference between the two sources influences the COP. The higher the temperature difference is, the higher the COP is. To assess the performance of the heating/cooling system over an entire season, the seasonal performance factor must be considered.
Parameter |
Units |
Min |
Max |
References |
Heat exchanger efficiency (plate heat exchanger) |
% |
69 |
91 |
|
Heat transfer coefficient (plate heat exchanger) |
W/(m² K) |
2500 |
8000 |
|
Coefficient of Performance (COPH) for heating |
- |
3 |
5 |
|
Seasonal performance factor (SPFH) for heating |
- |
4 |
5 |
|
Coefficient of Performance (COPC) for cooling |
- |
3.9 |
|
|
Seasonal performance factor (SPFC) for cooling |
- |
4 |
6 |
Links to related topics and similar reference projects
Processes/ technologies |
Reference |
Low grade heat recovery from MBR effluent and reuse |
NextGen case study Athens |
Low grade heat recovery from AnMBR effluent and reuse |
Ultimate case study Tain |
Case studies “Westland” (NextGen) and "Nieuw Prinsenland" (Ultimate) |
Case Studies applying the technology
Publications
- Bailey, O., Zlatanovic, L., van der Hoek, J., Kapelan, Z., Blokker, M., Arnot, T., Hofman, J., A stochastic model to predict flow, nutrient and temperature changes in a sewer under water conservation scenarios, 2020
- Banks, D., An introduction to thermogeology: ground source heating and cooling, 2012
- Brandenburger Liner GmbH, BB Heatliner, 2021
- Brunk, M., Seybold, C., Osebold, R., Beyert, J., Vosen, G., Dezentrale Wärmerückgewinnung aus häuslichem Abwasser, 2013
- Buri, R., Kobel, B., Energie aus Kanalabwasser - Leitfaden für Ingenieure und Planer, 2005
- Cecconet, D., Raček, J., Callegari, A., Hlavínek, P., Energy recovery from wastewater: a study on heating and cooling of a multipurpose building with sewage-reclaimed heat energy, 2020
- Cipolla, S., Maglionico, M., Heat recovery from urban wastewater: analysis of the variability of flow rate and temperature in the sewer of Bologna, Italy, 2014
- Elías-Maxil, J., Hofman, J., Wols, B., Clemens, F., van der Hoek, J., Rietveld, L., Development and performance of a parsimonious model to estimate temperature in sewer networks, 2017
- Kim, J., Hofman, J., Kenyeres, I., Poor-Pocsi, E., Kleyböcker, A., Heinze, J., Kraus, F., Soares, A., Paissoni, E., Vale, P., Palmer, M., Bloemendal, M., Beernink, S., Ros, S., Hartog, N., Frijns, J., D1.4 (2022) New approaches and best practices for closing the energy cycle in the water sector, 2022
- Kim J., Lanham A., Hunt A., Jotcham N., Williams H., Hofman J., D1.8 (2022) Greenfield implementation in Filton Airfield, 2022
- Soltani, R., Dincer, I., Rosen, M., Comparative performance evaluation of cascaded air-source hydronic heat pumps, 2015
- Torres Tamayo, E., Díaz Chicaiza, E., Cedeño González, M., Vargas Ferruzola, C., Peralta Landeta, S., Heat transfer coefficients and efficiency loss in plate heat exchangers during the ammonia liquor cooling process, 2016
- Wanner, O., Panagiotidis, V., Clavadetscher, P., Siegrist, H., Effect of heat recovery from raw wastewater on nitrification and nitrogen removal in activated sludge plants, 2005